I never thought that all those times I had to desolder and resolder bad solder joints at my last job would actually be useful for anything. Until now. Maybe I should back up a bit. At the makerspace where I used to work, we taught kids how to solder using these cute robot badges.
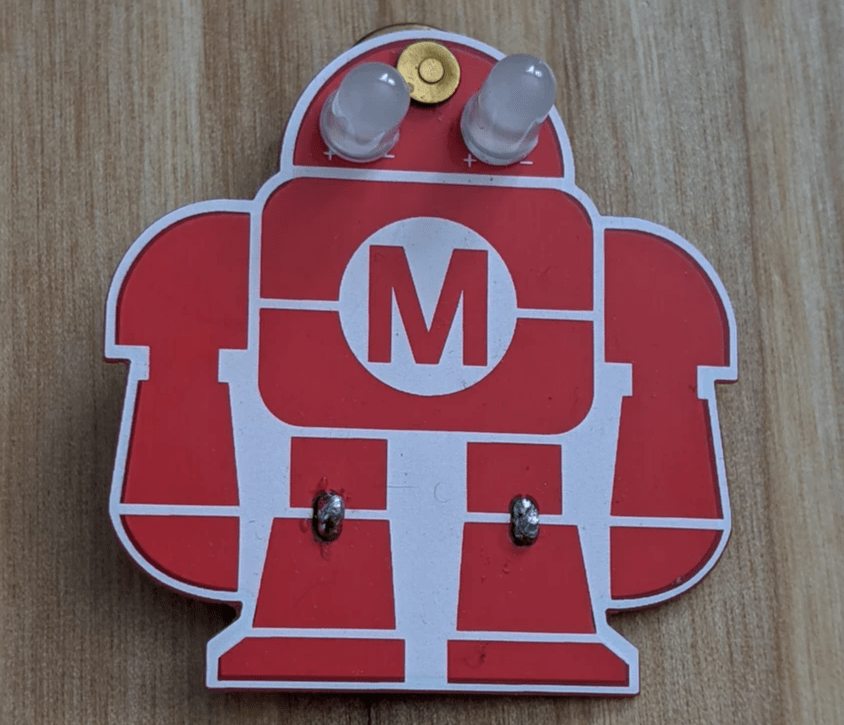
It wasn’t uncommon for there to be bad connections made due to excessive blobs of solder. We were dealing with younglings, after all. If the board hadn’t been completely melted, we could usually reverse the damage and get the robot to blink again. I quickly became a wizard at desoldering using copper wick and desoldering pumps.
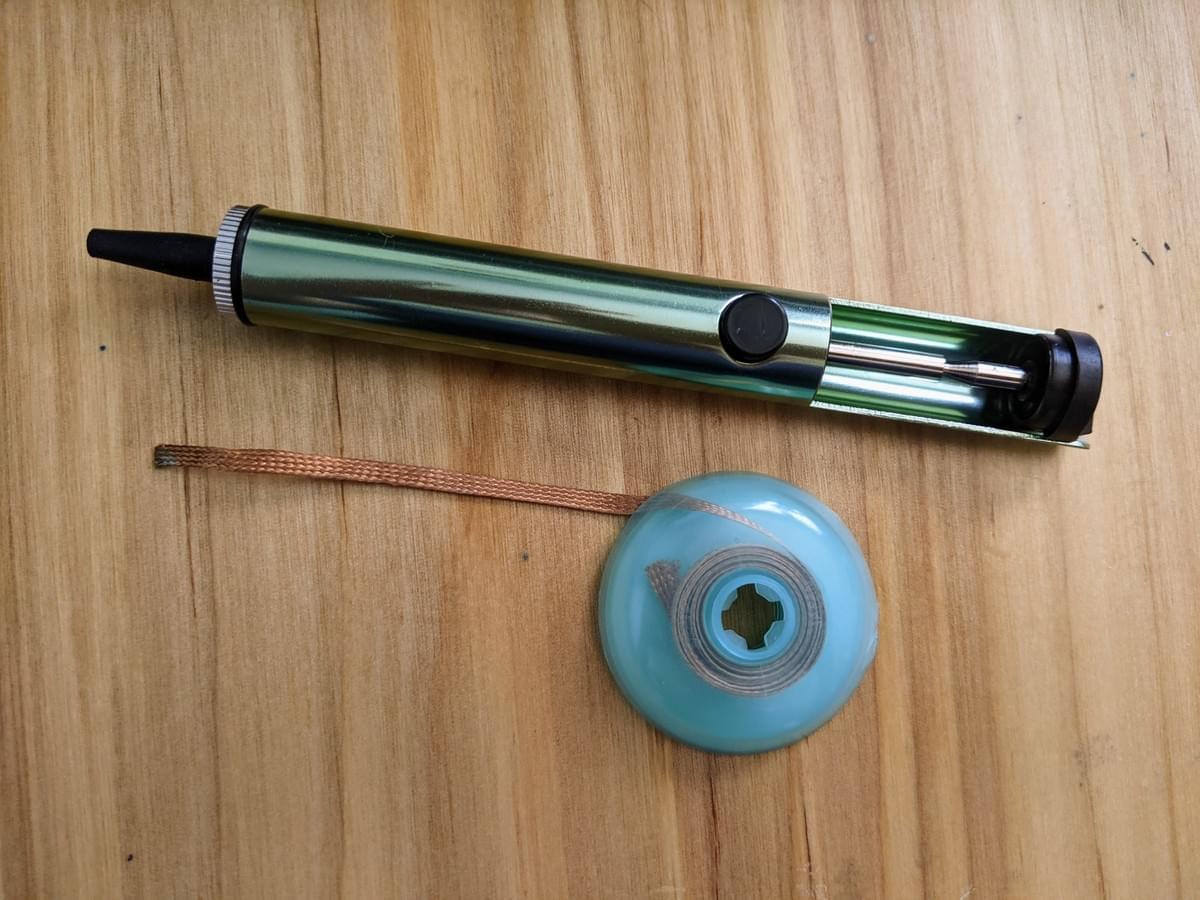
Flash forward to last weekend. As I do on most Sundays, I started a load of laundry. Only thirty seconds into the cycle, the washing machine protested with a cacophony of alarms, error codes flashing across its display. Now, this has been a constant battle with our washer and usually a quick rap over the control panel area was enough to knock it back into operation. I can’t really blame it for being sluggish. We inherited it from my Mom who probably bought it sometime around 2005. Clearly, it was tired of my brute force tactics and resumed its protests as soon as I tried to restart the cycle. To add insult to injury, it also decided to hold my wet laundry hostage by not unlocking the door. At this point, I did what anyone would do and exercised my Google-fu to find a solution. After reviewing many forums and videos, it looked like there might be some bad relays on the control board. We first took the board to our local appliance supply store where we found out that we could replace the entire board. Unfortunately, the board wasn’t in stock and ultimately would have cost us close to $600 to replace. Some clever person out there posted a slideshow on how to replace just the relays on the board and what parts to buy so we then explored that option. The relays were cheap and my husband ordered them as soon as he found the parts. I couldn’t wait to get them installed.
It was a simple matter to desolder the two relays we thought had gone bad. Upon opening one of them up, sure enough, we saw some carbon char.
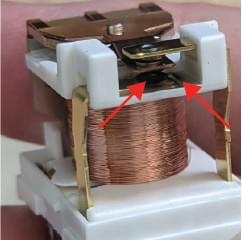
The other wasn’t in bad shape so we just stored it in case we needed a spare at some point. Excitedly, I had the husband unit re-install the board. We punched in a short cycle on the front console and…
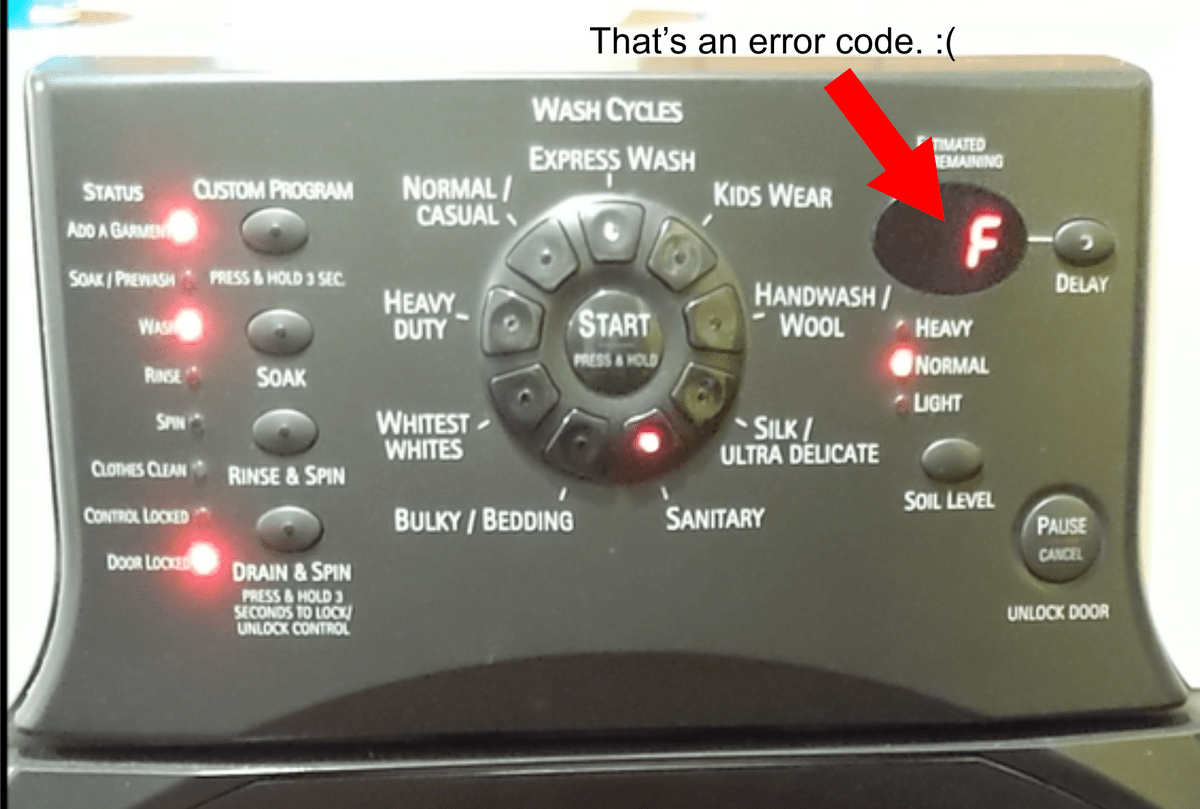
Yay alarms. Again. I was so disappointed. I really thought this would fix the problem. It did fix the door latch issue, however. Now the washer couldn’t hold our wet clothes hostage ever again. Take that, washer! But, there was still some sort of hang up right before it went into spin mode. I thought that maybe one of the other three remaining relays might have gone bad so I went ahead and ordered replacements. The day they arrived, I excitedly brought out the soldering iron and got to work. After a few minutes, they were soldered to the board and ready to go. The husband unit reinstalled the board and we anxiously ran another short cycle. Holding our breaths, we waited. And then…
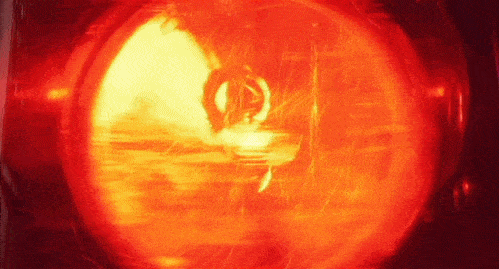
Curses! I went back and checked all the wires, including the ones leading to the other control board that controls the motor. Nothing seemed loose or bad. The hubby knocked tentatively on the laundry room door and said, “Let it go. It’s okay. How about we get some black mushroom chow mein for dinner?” It was clear that I had lost this battle.
I wish I could tell you that this maker had triumphed in the face of adversity. I wanted to share my successful battle against our societal norms that are so quick to dispose of our failing appliances. Even though that wasn’t the case, the fact remains that I tried. As disappointing as this experience was, I learned a lot. I learned how relays work and how to find the emergency door release on a washing machine. I even got to practice soldering and desoldering again. And you know, this whole experience has taught me to be a little bit more fearless when it comes to doing repairs around the house. We also got a beautiful scratch-n-dent washer out of the whole ordeal.
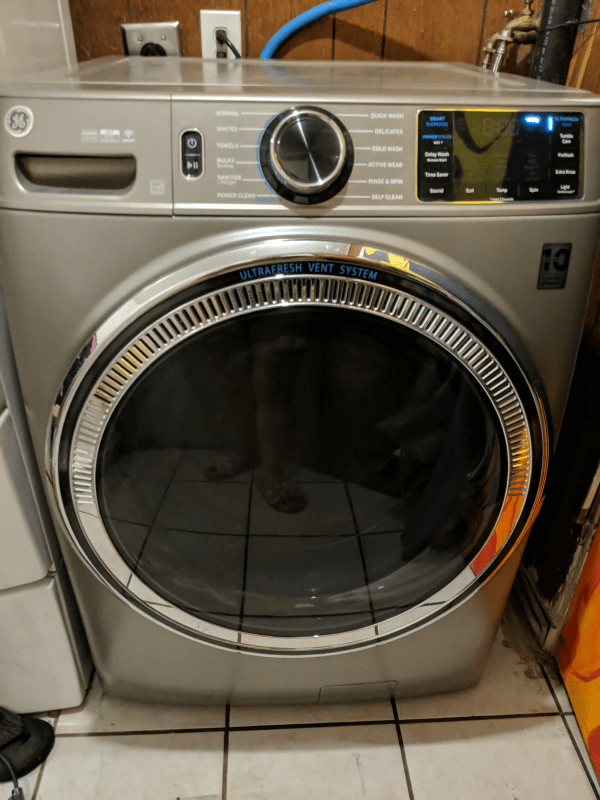